PIND
Built by the Experts
PIND
For reliability testing of all types of Ics / Relays / switches and hybrid electronics , detect the particles with our PIND Felix system.
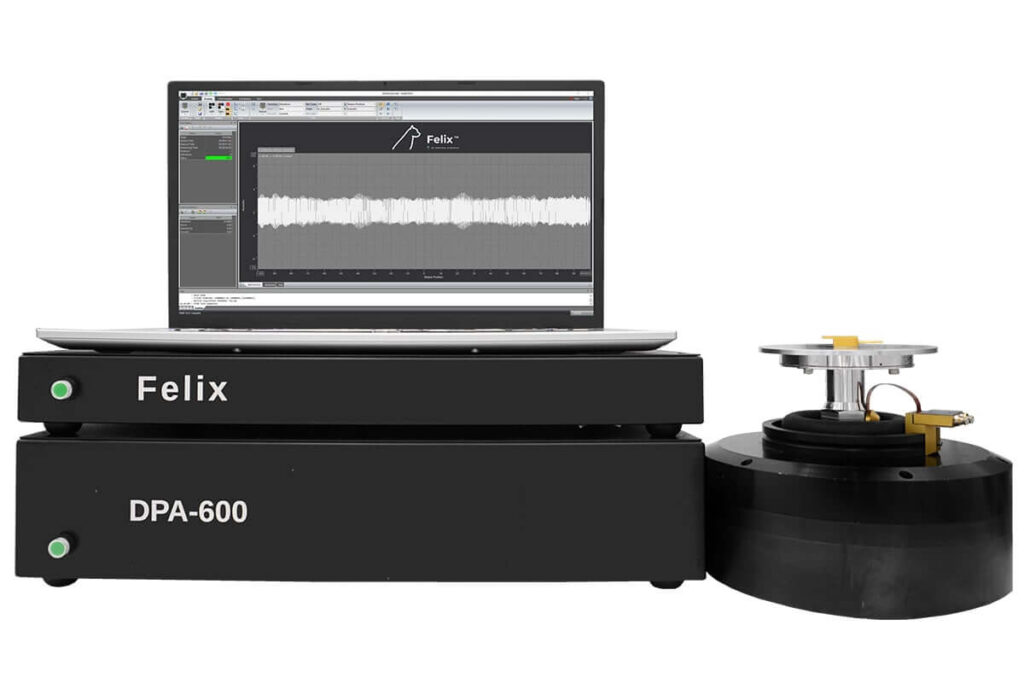
For over fifty years, Spectral Dynamics Inc. has given users simple, reliable and inexpensive tools to perform Particle Impact Noise Detection (PIND) testing to increase the reliability of electronic components.
The PIND FelixTM is the most advanced system available. Combining sensors that monitor and display the shaker motion with computer generated control to correct for changes in test conditions, the PIND FelixTM test system generates accurate and repeatable test conditions while meeting or exceeding all of the globally recognized test specifications.. The PIND FelixTM is truly a technology that the industry has been waiting for.
To provide always the best to our customers, Spectral Dynamics Inc decided in 2019 to discontinue the manufacturing, marketing and sale of the Spectral Dynamics former PIND Model 4511. Any representation by others that a similar or like product with the same features, functions or model number advertised or available for sale by the Spectral Dynamics USA or an affiliate of Spectral Dynamics is an unauthorized representation by such parties.
Support and services are still available for all Spectral Dynamics PIND systems including PIND FelixTM, PIND 4511 and PIND 4501 in our offices in the USA and France (for Europe).
The PIND Felix™ System has been designed to detect loose particles in electronic components. The system is programmable to provide speedy and precise automatic testing in accordance with the various standards. The interactive interface allows the operator to enter the desired stored test sequence and to control the test with ease.
The solution is completely designed by Spectral Dynamics. As this system is designed, manufactured, and built by Spectral Dynamics the quality of both components and build is controlled.
The PIND FelixTM is composed of:
- Precision Shaker with a crystal sensor system
- DPA600 digital Amplifier and FelixTM controller system
- Computer system with FelixTM software
- STU (Sensitivity Test Unit) unit to verify that the system is functional.
The system performs five major tasks:
- Vibrate a test article
- Shock a test article
- Detect any particle contaminants within the cavity
- Display the detected impact signals created by the loose particles
- Record the motion environment and the acoustic signals detected
The controller driven shaker provides shock and vibration motion of the test article. The impact sensor detects signals generated by a loose particle within the cavity of the test article, converts the physical energy into electrical energy which is passed through the cables to the amplifier and detection circuitry within the controller. Indication of the presence of loose particle detection occurs when the Acoustic Impact signal exceeds the programmed threshold limit.
Key features of the PIND FelixTM solution:
- Sensors
Depending of the test, Spectral Dynamics can supply single crystal or multiple crystal sensors. All our sensors have a complete Faraday shield around each crystal to protect the sensor from unwanted stray electrical signals. The embedded accelerometer allows monitoring and display of the actual shaker motion with computer analysis and correction for any changes in test conditions.
- Shaker
The unique shaker creates accurate “Active Shocks” with adjustable shock levels by controlling the velocity of the shaker head and correcting for device differences prior to impact
- Advanced software (Windows 10)
PIND FelixTM software allows for data collection of the vibration, shock, and acoustic channels. Each type of signal can be replayed for more in depth understanding of the interactions between the acoustic noise and the motion environment. Visual and audio particle detection are integrated to easily control your component. The software is compatible with tools like Microsoft Office. Reports for presentation or printing are simple to do.
- PIND testing according to international standards and internal process
The PIND FelixTM easily exceeds the requirements of all military standards for PIND testing (U.S. MIL-STD-883, 750, 202,39016D). It is also fully programmable to your own specifications if so required.
Our high frequency acoustic test monitors for loose particles moving inside high reliability internal cavity electronic components such as relays, transistors, integrated circuits, and switches – particles that have the potential of causing short circuits and serious malfunctions in system operations.
A shaker is used as a linear motor to excite loose particles to move within the component cavity. Upon striking the lid of the cavity, some of the particle kinetic energy is converted to a wide band acoustic pressure wave that travels through the lid, through the attachment media and onto the top surface of the Impact Detection Sensor.
The acoustic wave is detected by the sensitive ultrasonic crystal or crystals within the sensor and is converted into an electrical signal. To keep the particle moving, a very accurate shock, generated internal to the shaker and controlled by the computer, monitoring the motion of the sensor, is employed.
In the PIND Test, the particles are never measured directly. As the loose particles are placed in motion with a vibration, shock, the system then detects the impacts of those particles as they contact the lid of the cavity.
To learn more about the application, download our brochure.
Shaker options
4501-M230 Heavy duty vibration and shock shaker
4501-M230R Heavy duty shaker with wide pulse anvil included
4501-M230D Heavy duty shaker with two magnets
Sensor options
100-S140C/A Single crystal sensor – 22 mm
100-S140C/AL Single crystal sensor – 50 mm
100-3S155-60 Multiple crystal sensor – 60 mm – Three crystals
100-5S155-4 Multiple crystal sensor – 100 mm – Five crystals (1 in center with 4 mounted in a square at 50 mm)
Mounting options for components
There are two mounting mediums of the component on sensor:
- Acoustic gel couplant
The couplant provides both excellent acoustic transmission as well as limited adhesion for keeping the device in good contact with the device under test.
- Double sticky dots
Spectral Dynamics provides dots in several sizes. The doubled-sided dots provide excellent adhesion and good acoustic transmission. The transmissibility of the dot is less than the couplant by about 10% (1 dB).
Other options
Remote control box
The USB box for remote control can be used by the operator to:
- Load a test from the setup library
- Start the current or selected test
Shaker support
Need to isolate the shaker from your desk? Our team developed a dedicated support to perform your test anywhere.
Transport case
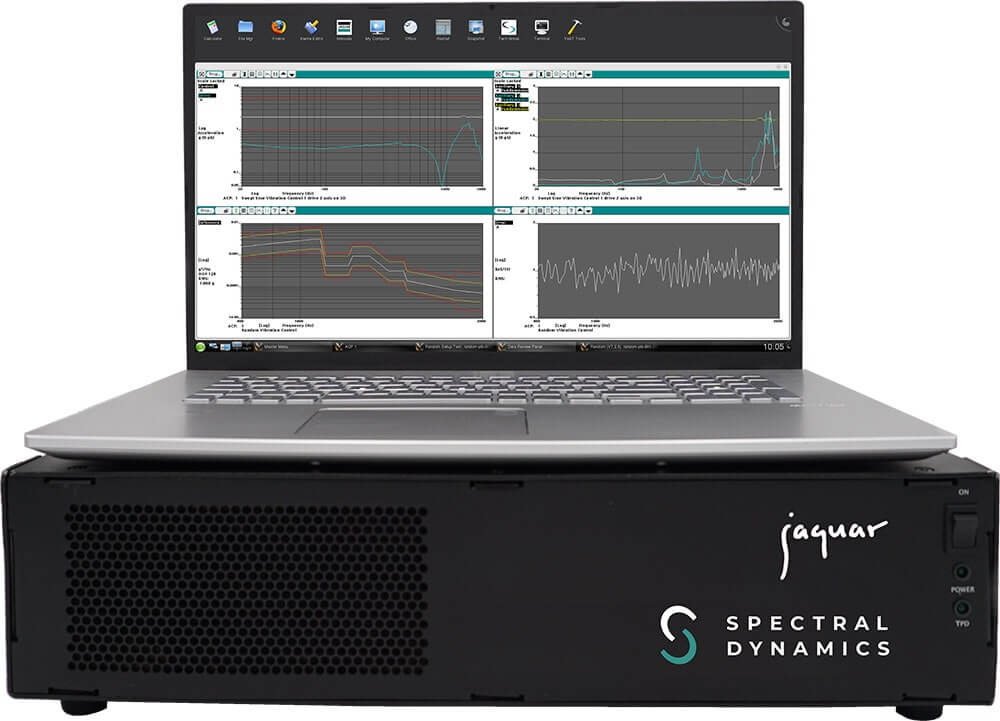
2. Jaguar™ : Powerful Acoustic and Vibration Controller for single or multiple outputs
When your Advanced applications need the most powerful controller available, the Jaguar™ is the ultimate in controller solutions.
When your controller applications demand multiple axis control and analysis, Spectral Dynamics has the solution. The Jaguar™ is configurable up to 98 control channels and over 550 response channels. Thanks to our Patented Adaptive Control Algorithm and our unique hardware architecture, the Jaguar™ stands alone as the Premier closed loop vibration and acoustic controller available on the market today.
The Jaguar™ is the most powerful single or multiple axis controller on the market today. We incorporate our patented Adaptive Digital vibration control technology for data acquisition and vibration as well as acoustic control. Our technology protects your test article and the test system while allowing for the ultimate in response delivering you the confidence in test results you desire.
Key features:
From 8 to 588 input channels
Our unique and powerful hardware architecture allows expansion to hundreds of channels without sacrificing signal processing performance.
Up to 98 control channels
With the powerful design of Jaguar™, you have the option to configure up to 98 control channels at the same time. All the channels can be used as control channels.
Spectral Dynamics Adaptive Control Algorithm
The JaguarTM uses an advanced Adaptive Control method, which is patented and declared to be a fundamental and revolutionary control method by the European and US patent offices. The adaptive control updates the system model as part of the multi-dimensional optimization used by the underlying optimal control method. These integrated control methods permit to reach the best control performance on the market for any test conditions.
Our technology protects your test article and the test system while allowing for the ultimate in response delivering you the confidence in test results you desire.
Accuracy
The JaguarTM is the only system in the world capable of changing the input ranges during a test with no adverse effects on the data. This occurs in our Sine or Random applications ensuring optimal use of the available dynamic range.
MIMO Capabilities
MIMO (Multiple Input – Multiple Output)
The JaguarTM has the power to recreate multiple degree of freedom environments in your test laboratory. Applications as diverse as vibrating a complex configuration of electronics in 3 axes simultaneously, driving a very heavy structure in one axis while sharing the load over many shakers or even recreating 6 DOF movement at each of the four wheels of an automobile may now be accomplished with the Jaguar™ MIMO application.
The Jaguar™, well known throughout the world for advanced vibration controller testing, also has a strong application success for acoustic control technology. The Jaguar™ is unmatched in its ability to control and analyze advanced test configurations when performing Direct Field Acoustic Testing (DFAT) for Satellites. Contact local Spectral Dynamics sales representative to find out more about our DFAT capabilities and experience as well as see the detail below MIMO Random acoustic Module.
The JaguarTM solution provides a complete software suite for all your applications.
MISO Control software (Multiple Input Single Output)
Tests configurations with multiple input and requiring only one output drive, can be configured easily with the Jaguar™.
Sine Module
The main analysis of the test consists in using tracking filter to bandpass the desired data, synchronizing the center frequency of the bandpass filter and locking it to the drive frequency. Our team is proud to provide one of the best tracking filters with the JaguarTM solution.
Random Module
The purpose of random excitation is to expose the test article to all frequencies, all phases, and all amplitudes in a truly random nature. The only condition to this is the customers shape must be produced and maintained, without losing the true random nature of the energy.
Shock
The JaguarTM uses patented adaptive control algorithm with transfer function updating and coherence smoothing to accurately and quickly compensate for non-linearities or time-varying changes in the dynamic load.
Mixed mode (Sine on Random / Random on Random / Sine & Random-on-Random)
The mixed mode consists in combining broadband, narrow band and tones to perform vibration tests.
MIMO Control software (Multiple Input Multiple Output)
As a majority of vibration testing is performed with single shaker excitation systems, conditions often exist where single excitation is not appropriate to achieve the desired test control and results. For these applications, Spectral Dynamics has developed a MIMO applications software suite to simulate the “real world” and allow a multiple channel input while allowing for multiple output drive generation.
MIMO Random Module
MIMO Random provide digital real-time closed loop shaker control for production testing, design qualification, and reliability testing applications. The system allows the definition, simulation, and closed loop control of random vibration excitation of a system with multiple exciters.
MIMO Sine Module
During manufacturing and use, all products encounter stress. MIMO sine tests are performed on both prototype and production-line products to ensure that the product will survive actual production and in-use conditions. MIMO sine vibration environments generally consist of a single sine wave frequency that changes frequency over time at several driving (excitation) points.
MIMO Shock Module
Do you have a need for closed loop control shock testing with multiple vibration actuators? Our MIMO Shock application is the solution.
MIMO Replication Module
This application allows the replication of field measured time history vibration data. Real vibration environment can be played back and controlled on the test system in a laboratory environment.
MIMO Random acoustic Module
Closed-loop acoustic tests are typically performed on products to ensure that the product will survive actual in-use conditions. Random acoustic environments are characteristically non-repetitive in time, the energy is generally present at all frequencies over a frequency range. This acoustic environment can accurately simulate many real-world operating conditions.
The JaguarTM can generate a wide range of random acoustic environments to satisfy nearly any commercial, industrial, or military test requirement. For instance, Direct Field Acoustic Testing (DFAT) for satellites can be performed thanks to the Spectral Dynamics’ MIMO random acoustic application.
Applications licenses
Spectral Dynamics offers you several options in configuring your suite of software control and application modules. The licenses can be configured with your original system or purchased at a later date.
MISO control licenses
Random
Sine
Sine Track resonance Dwell
Classical Shock
Shock Synthesis Waveform Generation and SRS
Mixed mode
Acoustic
MIMO control licenses
MIMO Random
MIMO Swept sine
MIMO Waveform replication
MIMO Shock
MIMO Acoustic
Analysis
Transient Capture
Signal analysis
Waveform processor
Other Software Options available for the Jaguar™
Spectral Dynamics offers specific options to help you to increase the efficiency of the test from the definition to the report.
– Throughput disk: Time record and storage
– Advanced data conversion and plots
– Rectangular and Hybrid control feature (MIMO applications)
– I/O Transformations feature (conversions between different coordinate systems for MIMO applications)